Dr. Anoop Kumar Sinha
Postdoctoral Researcher, ETH Zurich - Singapore ETH Centre, Singapore
Roboticist | Mechatronics | Inventor | Researcher
PhD - Robotics and Mechatronics @ NTU Singapore
M.Tech - Mechatronics @ Indian Institute of Technology (IIT), Patna India
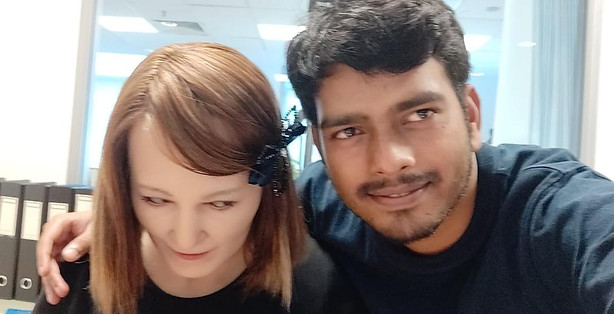
CV
Dr. Anoop Kumar Sinha
Postdoctoral Researcher, ETH Zurich - Singapore ETH Centre, Singapore
PhD- Robotics and Mechatronics
E-mail: anoop.ihpc2023@gmail.com
Phone: +65 91358631
About
It took a dream by few thoughtful humans like Czech novelist Korel Capek and the science fiction writer Isaac Asimov to actually think of a dream machine (robot) that could assist humans and today it’s a reality. I too believe in seeing such seemingly impossible dreams and then making them possible with all my strength. I specialize in robotics, automation, and mechatronics. I love designing, developing and manufacturing new systems that could be used for the social welfare of the people and society as a whole. My competencies are in design, sensorization, simulation, fabrication, and control in robotics. My scientific interests are in humanoid robotics, healthcare & assistive robots, human-robot interaction, cobots, virtual and augmented reality, UAVs, sensors & actuators, soft & stretchable robotics, and smart materials. I’m comfortable working on multidisciplinary teams or in being an “army of 1”.
Education
Doctor of Philosophy in Robotics and Mechatronics
Nanyang Technological University Singapore 2018- 2022 (Degree awarded on 31 May, 2023)
– School of Mechanical and Aerospace Engineering
– Specialization: Robotics and Mechatronics
– Lab: Institute for Media Innovation and Centre for Augmented and Virtual Reality
– Thesis Title: Towards a Sensorised Robotic Hand-Arm System for Humanoids
– Advisors: Nadia Magnenat Thalmann, Cai Yiyu, Wai Yee Yeong
– GPA: 4.33/5
Master of Technology in Mechatronics Engineering
Indian Institute of Technology (IIT) Patna (Bihar) India 2015 - 2017
– Department of Mechanical Engineering
– Specialization: Mechatronics
– Lab: Robotics and Automation Laboratoty
– Advisor: Karali Patra
– GPA: 9.15/10
Bachelor of Technology in Mechanical Engineering
Uttar Pradesh Technical University, Lucknow (Uttar Pradesh) India 2009 - 2013
– Institute: Feeroz Gandhi Institute of Engineering and Technology, Raibareli
– B.Tech thesis: Pipeline Inspection Robot
– Relevant Coursework: Engineering Mathematics, Thermodynamics, Heat transfer, Fluid Mechanics and Hydraulic Machines, Theory of Machines, Design of Machine Elements, Strength of Materials, Manufacturing Science, Material Science and Industrial Engineering
– Percentage: 74.26
Experience
Professional Experience
Postdoctoral researcher, ETH Zurich - Singapore ETH Centre (SEC), Singapore June 2024–Present
– Lead and coordinate the research activities of a large scale RehabGym project which intends to bring advanced
rehabilitation devices such as Rehandybot, MyoGuide, and H-MAN from hospitals to patients home.
– Supervise the RehabGym project research engineers and PhDs and advice them for successful completion of the project.
– Take charge and handle the administrative activities of the RehabGym project.
– Brainstorm new ideas for potential follow-up projects.
– Research proposal writing and applying for grants.
– Build strong connections with scientists and researchers globally and collaborate on new projects.
Scientist, A*STAR, Institute of High Performance Computing, Singapore Apr 2023–May 2024
– Coordinate the activities, develop ideas, and contribute hands-on in the department research.
– Research proposal writing and applying for grants.
– Sharing research findings in high impact journals and securing patents for innovative research.
– Building connections with scientists and researchers globally to cultivate novel research concepts with technological
and innovative significance.
– Formulating research proposals and grant applications that offer substantial social and economic advantages.
Research Associate, Nanyang Technological University, Singapore Nov 2022–Mar 2023
– Helped setup the Bio-electronics workspace within the Biological Processing lab NTU.
– Developed an in-house setup for conducting bio-electronics measurement.
Supervisory
Co-mentored Dissertation, Nanyang Technological University, Singapore Sep 2021–Mar 2022
– Co-mentored two undergraduate students towards their final year project with my PhD advisor.
Research Supervision, Nanyang Technological University, Singapore Aug 2020–Dec 2020
– Supervised undergraduate intern research project on prosthetic hand design and machine learning implementation on EMG data. The research project was conducted at Institute for Media Innovation, Nanyang Technological University, Singapore.
Project Supervision, Young Innovators Challenge, Singapore Mar 2021
– Supervised students from Methodist Girls’ School on the project assistive learning devise for ADHD students. Leading the team to win best creativity award in the Singapore Young Innovators Challenge 2021.
Grant Writing
Robotic lab Indian Institute of Technology, Patna Oct 2017
– Co-written a proposal for research grant with my M.Tech supervisor on, “Fabrication of Soft Sensors, Organ-On-A-chip, and Lab-On-A-chip devices using cryogenic micromachining of soft materials.”
– A grant of INR 5,000,000 (≈ $65,000) for 2 years was awarded by Department of Science and Technology (DST), India for our proposal.
Reviewer
– Invited Reviewer, IEEE/ ASME Transactions on Mechatronics Sep 2021
– Reviewer, MDPI Sensors Present
– Reviewer, MDPI Robotics Present
– Reviewer, MDPI Prosthesis Present
Research
Smart factory-Rolls Royce Oct 2023–Jan 2024
– The project involved creating a digital twin for the automated assembly and alignment of jet engine modules.
– A digital twin with a GUI for this assembly process was developed in Unity 3D.
– The digital twin and GUI enabled the user/worker to identify misalignments and deviations typically not visible to the human eye, allowing them to stop the process and correct the alignment issues.
Bioinspired Exosuit for Elderly July 2023–Sep 2024
– The project involved design and development of bio-inspired lower limb passive exosuit for enhancing strength and capability of elderly.
– Multiple physics-based designs were proposed by taking inspiration from the biological world and accommodating function sharing concept.
– The project also explored advanced materials and methods such as 3D printing or 3D knitting that can be used to fabricate these exosuits.
Neurophysiological Insights into Usability and User Experience of Smart Products with VR and AR Prototypes Apr 2023–May 2024
– Developing usability and acceptance protocols for new functions/features in smart products (specifically a smart wrist rehabilitation device for stroke-affected patients) designed to facilitate smart living in smart homes.
– A protocol leveraging the power of virtual reality (VR), tangible augmented reality (TAR), and user-specific neurophysiological data to assess the user experience and acceptability of these devices was developed.
– The protocol also involved the creation of UI/UX, virtual prototypes, and emotion categorization based on unique and authentic user neurophysiological data.
Multi-modal sensing palmtop Jan 2022–Mar 2022
– A novel design and a method for fabrication of a palmtop with 390 tactile pressure sensing nodes and 5 hydration sensing nodes was developed using aerosol jet 3D printing of Ag nanoparticles. The overall fabrication cost of the palmtop is <$10 and the overall fabrication time of the palmtop is around 6 hrs.
– The multi-modal sensing palmtop is then used to identify and classify different objects objects.
(Manuscript in preparation for submission in Wiley small. Impact factor 15.15)
Skin-inspired multi-point fingertip sensor for smart glove Oct 2021–Jan 2022
– Multi-point fingertip sensors were fabricated using advanced 3D printing.
– Sensors were characterized. Results indicate response faster than human skin (≈ 4 ms), high sensitivity, and ultra low hysteresis.
– Deep learning is used to identify the objects and direction of touch.
(Work published in Wiley Advanced Material Interfaces. Impact factor 6.147. Click here to read.)
MIDAS: Multi-sensorial Immersive Dynamic Autonomous System to improves motivation of stroke affected
patients for hand rehabilitation Sep 2020–Jan 2021 – Current rehabilitation devices have failed to motivate the patients enough to continue rehabilitation exercises.
– MIDAS is intended for stroke patients who suffer from light to mild stroke. MIDAS is lightweight and portable. It consists of a hand exoskeleton subsystem, a Virtual Reality (VR) subsystem, and an olfactory subsystem. Altogether, MIDAS engages four out of five senses during rehabilitation
– In our pilot study it was found that 60% of the scores of user experience are above 40 (out of 56). 96% Self Rehabilitation Motivation Scale (SRMS) rating shows that the participants are motivated to use MIDAS and 87% rating shows that MIDAS is exciting for rehabilitation.
(Preprint available at Arxiv. Click here to read.)
Measuring anthropomorphism of a new humanoid robot hand-arm system Sep 2019–Aug 2020
– Human-like kinematics and dynamics can improve the efficiency of human robot interaction (HRI) as such motions can be intuitively understood by human in an HRI task.
– A new method to measure kinematic anthropomorphism of robotic hand-arm systems is proposed.
– A new humanoid robot hand-arm system was designed and developed. The proposed method was used to measure anthropomorphism of our humanoid robot hand-arm system and compared with those of other humanoid hand-arm systems.
(Work published in Springer Nature International Journal of Social Robotics. Impact factor 4.31. Click here to read.)
Development of a bi-axial stretching device for dielectric elastomers (M.Tech thesis) Jul 2016–Aug 2017
– Developed an automatic setup capable of providing uniaxial, equibiaxial, and unequibiaxial stretching of Dielectric Elastomers (DEs) at controlled stretching rate. After stretching, DEs are used to make sensors, actuators, and generators with improved performance.
(Patent granted).
An Apparatus and Method for Cryogenic Micromachining of soft materials Sep 2017–Feb 2018
– Developed a closed chamber set up for cryogenic micromachining of soft materials under a temperature controlled environment. – Soft materials were cooled below their glass transition temperature and micro channels were machined onto the soft material.
– The soft material carrying the micromachined pattern of channels can be used to fabricate sensors, lab-on-chip, and body-on-chip devices.
(Patent application submitted. Grant pending.)
Human motion capturing and teleoperation of a humanoid robot Jan 2016–Apr 2016
– The lack of an effective, economical and a simple technique for teleoperation of humanoids is a barrier in exploring their full potential. In this project, our team reported a novel method for teleoperation of a humanoid robot using an exoskeleton for lower limb and upper limb.
– Human motion was captured using our exoskeleton and different walking patterns like slow walking, fast walking and jogging analyzed.
– The motion data captured using exoskeleton were applied to teleoperate khondo KHR humanoid robot.
(Work published in International conference MAMI 2018.)
Pipeline inspection robot (B.Tech thesis) Sep 2012–Apr 2013
– The central problem of this project was to think of an innovative design so that the robot can accommodate itself into pipelines of varying diameters.
– The design included a central element, a translating element attached to a spring, six small sized links and three connecting links which were comparatively longer. The spring enabled the robot to adjust in pipelines of varying diameters.
– There were six wheels actuated by DC motors and powered by batteries. The robot was wireless controlled by RF (2.4GHz) and equipped with night vision camera to provide real-time video on a computer screen.
Industry
Industrial Training at Diesel Locomotive Works Varanasi (Uttar Pradesh) India. Jul 2012 - Aug 2012
– Six weeks industrial exposure to different shops like Machine Shop, Light Machine Shop, Heavy Machine Shop, Heavy Weld Shop, Heat Treatment Shop, Loco Assembly Shop.
Industrial Training at Diesel Locomotive Works Varanasi (Uttar Pradesh) India. Jul 2011–Aug 2011
– Four weeks industrial exposure to different shops like Light Machine Shop, Heat Treatment Shop, Sub Assembly Shop, Traction Assembly Shop.
Teaching
Teaching Assistant, Nanyang Technological University, Singapore Aug 2019–May 2021
– MA 2072: Laboratory experiments
– FE 1073: Introduction to engineering and practices
– MA 3071: Control of vibration
Teaching Assistant, Indian Institute of Technology (IIT), Patna Jun 2016–Jul 2017
– SE 505: Mechatronics and Robotics Laboratory-I
– SE 506: Mechatronics and Robotics Laboratory-II
–Hands on experience industrial robots SCARA & ARISTO ,fire bird XI, humanoid robot, NI-DAQ, Micro controllers, hydraulic and pneumatic setup, CNC micromachining and sensors like thermocouple, Strain gauge, LVDT, Photo sensor, ultrasonic sensor etc.
Undergraduate Assistant, Feeroz Gandhi Institute of Engineering and Technology Sep 2011–Aug 2013
– KME 751: Measurement and Metrology Lab
– NME 352: Machine Drawing I
– KME 071: Additive Manufacturing
Leadership Positions Held in Extracurricular Clubs
Assistant Director of Academics, NTU MAE graduate students club Jul 2021– Apr 2022
Assistant Director of Career, NTU MAE graduate students club Jul 2020– Apr 2021
Vice President, NTU MAE graduate students club Jul 2019– Apr 2020
Assistant Director of Academics, NTU MAE graduate students club Jan 2019– Apr 2019
Cultural Fest, Co-organizer, IIT Patna Anwesha annual cultural fest, co-organizer Jan 2017
Director, IIT Patna student gymkhana Jan 2016 – Mar 2017
Treasurer, IIT Patna student gymkhana Dec 2015 – Mar 2016
Event Manager, FGIET Raibareilly Kalpvaig annual sports fest Dec 2012
Event Manager, FGIET Raibareilly Kalpvaig annual sports fest Dec 2013
Skills
Robotics, Mechatronics, Robot design, Robot kinematics, Robot dynamics, Manipulation, Tactile perception, Sensors, Actuators, Sensor fabrications, Sensor physics, Humanoid robots, Rehabilitation robotics, Industrial robots 4-axis SCARA, 6- axis Aristo XT, Festo's hydraulic and pneumatic setup.
Software
– Extensive experience with LabVIEW, Simulink, Creo, AutoCAD, SolidWorks, 20-sim, Ansys, Origin, Matlab, and Processing. Programming language C, C++, Python.
– Extensive GUI development experience with Matlab and Processing.
– Some experience with ROS.
Mechanical Fabrication
–Extensive experience with CNC micromachining, CO2 laser cutting, 3D printing, and silicone molding.
–Some experience with manual milling and manual lathe turning. Some experience with SEM.
Electronic Fabrication
– Extensive experience performing circuit design/prototyping for digital and analog sensors: peizoresistive, capacitive, LVDT, LIDAR etc.
– Conceptualising novel sensor design and prototyping.
– Experience with data acquisition systems: NI-DAQ.
– Extensive knowledge of actuators: linear and rotary actuators, servos, hydraulic, and pneumatic.
– Experience with smart material actuators: dielectric actuators (DEA), shape memory alloys (SMA).
– Extensive experience with signal conditioning circuit design and prototyping.
– Experience with developing user interface for displaying sensor data.
– Extensive experience with Raspberry Pi, Arduino UNO, Mega, and Nano.
Hobbies
Travelling
Reading
Cartooning
Music
Publications
Patents
– Anoop Kumar Sinha and Karali Patra. (2017). A Stretching Apparatus and a Method of Stretching. (Indian Patent No. 345777). [Link]
– Anoop Kumar Sinha and Karali Patra. (2018). An Apparatus and a Method for Cryogenic Machining of Polymer Materials. (Indian Patent Application No. 201831036316). [Link]
– Anoop Kumar Sinha, Yiyu Cai, Gou Liang Goh and Wai Yee Yeong. (2023). An ultra low cost, near human skin sensitivity fingertip sensor. (International Patent Publication No. WO2023204766A1).[Link]
Reviewed Journal Articles
– Sinha, A.K., Goh, G.L., Yeong, W.Y. and Cai, Y., 2022. Ultra-Low-Cost, Crosstalk-Free, Fast-Responding, Wide-Sensing-Range Tactile Fingertip Sensor for Smart Gloves. Advanced Materials Interfaces, 9(21), p.2200621. (Impact factor: 6.147)[Link][Video]
– Sinha, A.K., Thalmann, N.M. and Cai, Y., 2023. Measuring Anthropomorphism of a New Humanoid Hand-Arm System. International Journal of Social Robotics, pp.1-23. (Impact factor: 4.312)[Link] [Video 1] [Video 2]
– Kow, F.C.S.F., Sinha, A.K., Ming, Z.J., Songyu, B., Kang, J.T.J., Jeffrey, H.Y.J., Mihaleva, G., Thalmann, N.M. and Cai, Y., 2022. MIDAS: Multi-sensorial Immersive Dynamic Autonomous System Improves Motivation of Stroke Affected Patients for Hand Rehabilitation. arXiv preprint arXiv:2203.10536. [Link].
– Goh, G.L., Goh, G.D., Nguyen, V.P., Toh, W., Lee, S., Li, X., Sunil, B.D., Lim, J.Y., Li, Z., Sinha, A.K. and Yeong, W.Y., 2023. A 3D Printing-Enabled Artificially Innervated Smart Soft Gripper with Variable Joint Stiffness. Advanced Materials Technologies, 8(24), p.2301426. (Impact factor: 6.8)[Link][Video1][Video2]
– Sinha, A.K., Goh, G.L., Cai, Y., and Yeong, W.Y., 2024. Skin Inspired, High-Resolution, Intelligent Aerosol Jet 3D-Printed Palmtop with Multisensory Integration. (Under review in Wiley Advanced Intelligent Systems) (Impact factor: 7.4)
Conference Articles/ Presentations
– Sinha, A. K., Sahu, S. K., Bijarniya, R. K., and Patra, K. (2017). An effective and affordable technique for human motion capturing and teleoperation of a humanoid robot using an exoskeleton. In 2017 2nd International Conference on Man and Machine Interfacing (MAMI) (pp. 1-6). IEEE.[Link]
– Rosen, D.W., Choi, C.Y, Sinha, A.K., 2023, October. Product Architecture Design Benefits of Additive Manufacturing. In 2nd International Conference on Design for 3D Printing. (conference presentation)
– Rosen, D. W., Choi, C.Y., and Sinha, A.K., 2024, May. Toward a Design Methodology for Configuring Assistive Wearable. Proceedings of the 18th International Design Conference (accepted for publication).
– Sinha, A.K., Rosen, D. W., and Choi, C.Y., 2024, July. Automated Usability and User Experience Assessment for Smart Products and Assistive Devices. Proceedings of the 31st International Conference on Transdisciplinary Engineering (accepted for publication).